Paints are the general term for materials applied to the surfaces of objects and forming a hard protective film; It is coated to decorate the surface of the object in question, to protect it or for different purposes (insulation, anti-rust, mould-proofing, heat resistance).
Paint Categories:
1. According to the paint type; water-based paint, solvent-based paint and powder paint etc. can be divided as .
2. In accordance with the construction method, painting, brush painting, spray painting, roller painting, dipping painting, electrophoretic painting, etc. can be divided as follows.
3. Painting, primer, intermediate paint, top coat paint, varnish, etc. in accordance with the construction process. can be divided as follows.
4. According to its function, it can be divided into painting, decorative painting, anti-rust painting, conductive painting, high temperature resistant painting, thermal insulation painting, fire retardant painting, waterproof painting, etc. can be divided as follows.
5. According to the use, paint can be divided into construction paints, tin paints, automobile paints, aircraft paints, electrical appliance paints, wood paints, bridge paints, plastic paints, paper paints, etc. can be divided as follows.
6. Paint for home use, interior paints, exterior paints, wood paints, metal paints, floor paints, etc. can be divided into:
7.According to the performance of the paint film, the paint can be divided into anti-corrosion paint, insulation paint, conductive paint, heat-resistant paint, etc. can be divided into:
8.According to the film-forming substances, paint, latex paint, polyurethane coating, epoxy paint, acrylic paint, alkyd paint, fluorocarbon coating, phenolic paint, vinyl coating, etc. can be divided into:
SÖZER MAKİNA has a long history in providing paint and coating production machines, and has provided equipment and turnkey projects to world-renowned and respected paint and coating production companies. We have rich experience in paint production, we can produce equipment and machines that are highly suitable for today’s technology of liquid/powder feeding, color-paste production, filling and automatic control systems. We also produce very successful machines in the field of grinding. So far we have developed crushing and grinding machines that significantly increase the grinding fineness and efficiency.
We also produce very successful machines in the field of grinding. So far we have developed crushing and grinding machines that significantly increase the grinding fineness and efficiency.
As SÖZER MAKİNA, we not only provide equipment, but also provide complete facility installation, engineering services, production expansion, project management, consultancy services and project design services to completely solve the difficulties in paint and coating production.
The machines we produce for the Paint Industry;
These are mixers that can be used both base-based and platform-mounted after a certain capacity. These are machines mostly used to disperse paints. They can be used with fixed boilers or mobile boilers. In addition to our standard models, they can be produced according to your projects in the capacity and engine power you desire. Frequency inverter technology allows stepless speed adjustment. In addition to the ability to rise and fall on their own body with an electro-hydraulic system, they also have the feature of mixing at a desired height. There are cooling engines adapted to the main electric motor that allow long-term operation at low speeds.
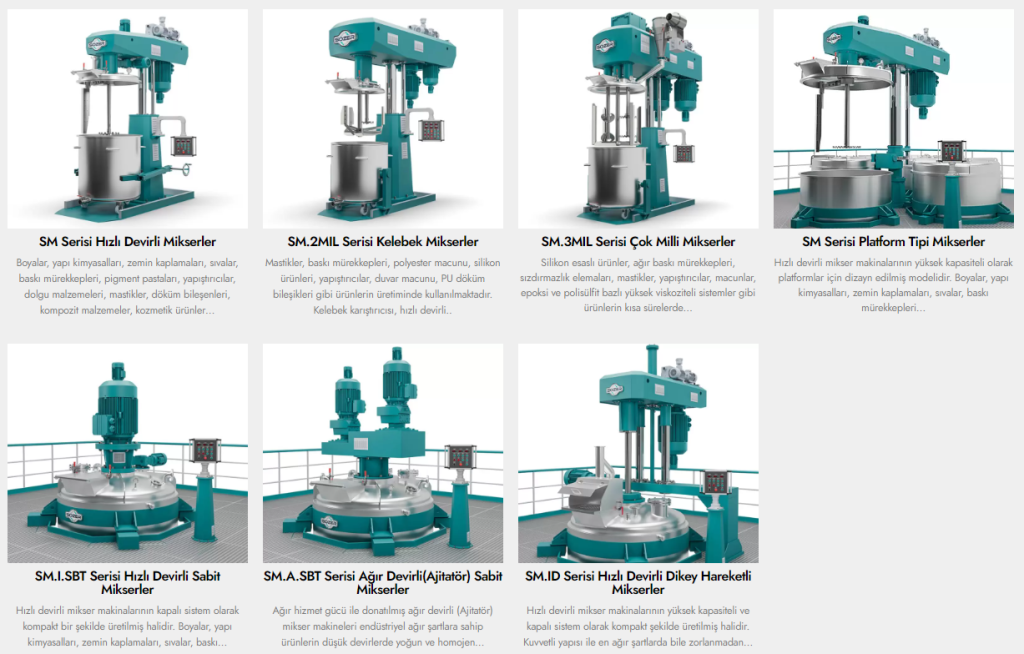
While the time-adjusted mixing feature is available as standard, the boiler side and bottom moving scraper system, mobile and automatic vacuum system, ex-proof design in ATEX Zone 1 EEx dIIB T4 standards, double-deck propeller, temperature measurement system, level of the product in the mixing tank are available to meet the requirements. automatic up-down feature of the mixer, weight measurement system, semi-automatic or fully automatic PC / PLC control system with recipe control, etc. Many other features such as are offered as options. There are options of various types and features such as butterfly mixer and two shafts.
The grinding basket with superior wet grinding feature used in the machine is completely designed to ensure high crushing of the product. It has the feature of completing the operation effectively in a short time thanks to its highly efficient product passage and its impeller, which works like a pump and is located under the grinding basket and contributes to dispersion. Effective heat control is provided by cooling both in the grinding basket chamber and on the boiler wall. All wet surfaces are made of stainless steel. The grinding beads in the grinding basket play a big role in this machine. They are steplessly adjustable with frequency inverter technology. In addition to the ability to rise and fall on their own body with an electro-hydraulic system, they also have the feature of mixing at a desired height.
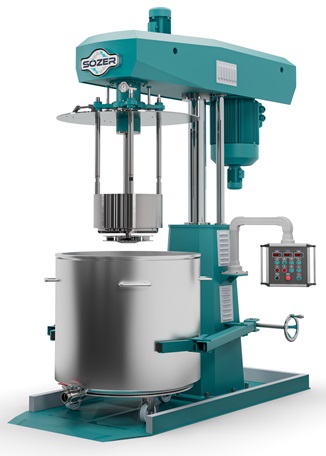
There are cooling engines adapted to the main electric motor that allow long-term operation at low speeds. Time-adjusted mixing feature and temperature measurement system are offered as standard. Movable and automatic vacuum system, ex-proof design in ATEX Zone 1 EEx dIIB T4 standards, weight measurement system, semi-automatic or fully automatic PC / PLC control system with recipe control are offered optionally.
There are two types of high-performance horizontal crushing systems used in the machine. Effective performance can be achieved in both systems as pin and disc systems, which can be selected according to the product to be crushed. Its completely closed, leak-proof design has been designed with a fast and effective transition structure for grinding powder raw materials in liquids at nanoscale. The machine can have PLC and standard control systems. Thanks to the PLC system, relevant operational data such as temperature, energy consumption, crushing process control and recipe management can be easily done. An effective passage and discharge of the crushed product is achieved by creating a perfect centrifugal effect with the dynamic separator feature in the mechanical seal system. If the system has pins, it is also possible to change the pins.
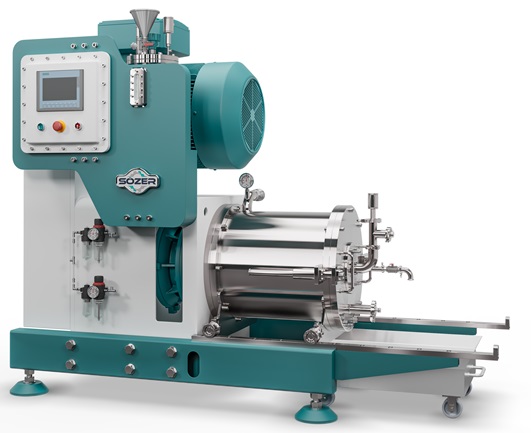
This feature is valid for disk systems. Ex-proof design in ATEX Zone 1 EEx dIIB T4 standards, recipe-controlled semi-automatic or fully automatic PC / PLC control system are optionally offered.
The machine has its own pump system suitable for its structure as standard. The level detection system in its own filling tank keeps the filling tank constantly filled by automatically switching on and off until the product in the production tank runs out. Weighing and filling quantity entries are made electronically with the help of the standard load cell and indicator system. The smart indicator system automatically calibrates each filling, allowing very precise filling. As a standard, all surfaces in contact with the liquid such as the machine boiler, filling nozzles, level measurement rod are manufactured from AISI 304-L quality stainless steel material.
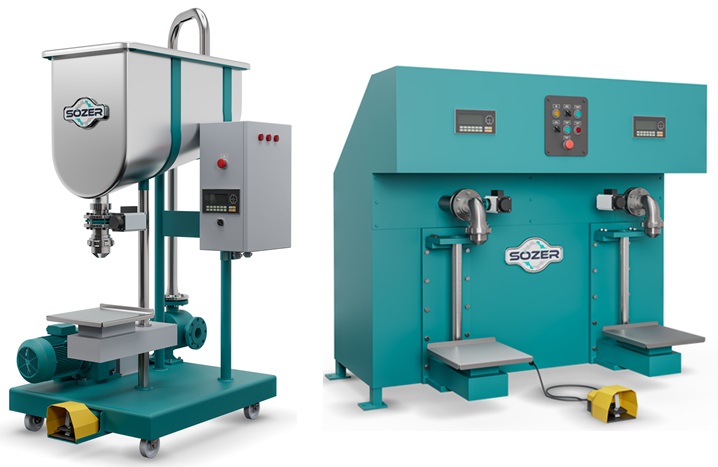
Two different diameter filling nozzles are provided with the machine to be used in small and large fillings. The machine is manufactured on a wheeled chassis as standard, so it can be pulled to the desired location. The height of the weighing pan where the empty container will be placed is adjustable.
The machine requires 6 bars of compressed air to operate. Nozzle systems of different sizes, box closing and conveyor lines, ex-proof design in ATEX Zone 1 EEx dIIB T4 standards, semi-automatic or fully automatic PC / PLC control system with recipe control are offered as optional features.
It is established for companies with a production capacity between 500 Tons/Year and 50,000 Tons/Year, depending on the need. Can be customized based on paint category and production requirements. The whole system includes advanced production technology with material feeding system, measuring system, disperser and milling system, cleaning system, automatic control system, automatic filling system, etc. It can be created with the combination of individual machines or the combination of an automatic production line. The entire system can also be designed and produced as Ex-Proof according to the properties of the materials. In this type of systems, raw material feeding is mostly carried out by automatic powder and liquid transportation systems.